Business & Finance
Inventory Management Tools Integrated with Document Approval Workflow
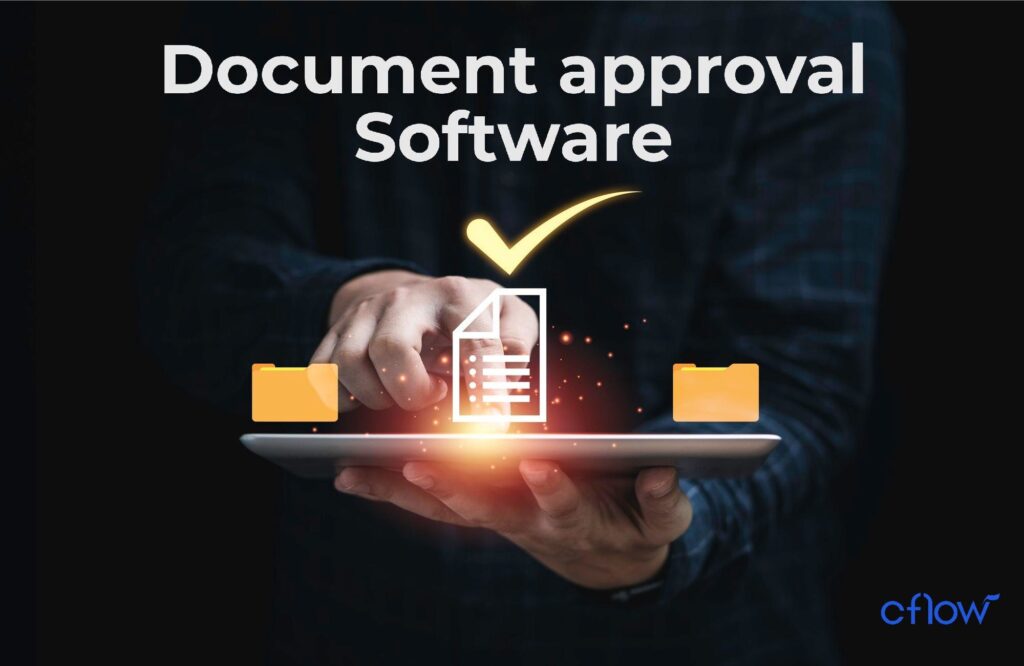
Managing stock and paperwork efficiently is critical. By using inventory management tools to track goods and materials, and combining them with a seamless document approval workflow, organizations can streamline operations and cut errors. These two systems work together—inventory tools handle stock levels and order tracking, while an integrated document approval workflow ensures all necessary paperwork (like purchase orders, stock transfers, and receipts) is reviewed and authorized quickly. Together, they help businesses move faster and stay organized.
Body
1. Why Integration Matters
- Reducing manual work: When inventory management and document approval workflows are separate, staff must juggle multiple systems. Integration saves time by automatically generating approval requests when stock is low or replenishment is needed.
- Improved accuracy: Automation cuts down on data entry mistakes like wrong item counts or missing signatures. This increases trust that stock levels and documentation are correct.
- Better visibility: Managers can see where inventory sits and what approvals are pending in one unified dashboard. This helps avoid lost orders or stockouts.
2. Key Features of Inventory Management Tools
An effective inventory management tool typically includes:
- Real-time tracking: View stock levels as they change, across locations or warehouses.
- Reorder alerts: Automated notifications when item quantities hit a threshold.
- Supplier information: Supplier details and lead times help forecast needs.
- Batch and serial control: For traceability of products or expiry dates.
- Reporting and analytics: Dashboards that visualize trends, turnover, or shrinkage.
3. Key Features of Document Approval Workflow
A document approval workflow should provide:
- Automated routing: Documents like purchase orders or stock requisitions move automatically to the right approvers.
- Custom approval paths: You can define who approves under what scenarios, for example higher-value stock requests go to senior staff.
- Tracking and reminders: Notified when approvals are pending, with escalation if delayed.
- Audit trails: Full logs of who approved what and when, ensuring compliance.
- Easy accessibility: Mobile or web access so approvers can act from anywhere.
4. How the Integration Works
a. Triggering Approval Requests from Inventory Events
When stock falls below a threshold, the system can generate a purchase order or internal stock requisition. That document is sent immediately into the approval workflow, with supplier details and item lists already populated.
b. Status Updates Flow Back to Inventory
Once a document is approved, the inventory system updates: stock is reordered, expected delivery dates recorded, and pending receipts flagged. If a request is rejected, staff receive feedback quickly, so they can adjust the order or provide additional justification.
c. Cross‑Function Coordination
Inventory or warehouse staff can upload receipt documents, delivery notes, or invoices to the approval workflow. These get approved by finance or operations before stock is marked as received, maintaining process discipline.
5. Benefits of Combined Solution
- Speedier process cycles: Approval requests are triggered automatically, reviewed promptly, and executed faster.
- Fewer errors and disputes: Unified records minimize mismatches between inventory records and associated documents.
- Financial control: Finance teams gain visibility over upcoming orders and budgets before purchase commitments.
- Compliance and audit readiness: Since every document passes through a traceable workflow, audits become easier.
- Scalability: As a company grows, workflows and inventory processes can be adjusted without new tools or rework.
6. Real‑World Use Cases
Retail or E‑commerce
Popular products often sell out quickly. When inventory dips below reorder level, an automatic PO is generated and routed for approval. Once approved, the system places the order and logs expected delivery, ensuring timely restocking and avoiding stockouts.
Manufacturing
Re-ordering raw materials is a regular task. The system tracks material levels, triggers purchase requests, routes them for approval, and then updates inventory when materials arrive—all in one seamless process.
Healthcare or Laboratories
These require tight control over inventory and strict chain of custody. Integrated flows assure that when sensitive supplies like medicines or test kits are used or reordered, proper approvals are in place and records are kept accurately.
7. Tips for Implementation
- Map your current process: Understand how inventory and approvals work today, especially thresholds, document types, and who is involved.
- Define clear rules: Set reorder levels, approval hierarchies, and conditions for automatic triggers.
- Train your team: Make sure warehouse staff, procurement, finance, and managers know when and how systems interact.
- Start small: Pilot the integration with selected items or departments before rolling out across the enterprise.
- Monitor and refine: Use performance dashboards to catch delays or bottlenecks and tweak rules as needed.
Conclusion
An integrated system that combines inventory management tools with an automated document approval workflow transforms how companies manage stock and paperwork. It cuts manual work, improves accuracy, speeds up decision‑making, and increases transparency. Whether in retail, manufacturing, healthcare, or beyond, linking stock-level tracking with document approvals creates a smarter, more agile operation. Companies embracing this fusion benefit from leaner processes, stronger compliance, and better financial control. If you’re looking to streamline procurement, improve inventory accuracy, or enhance operational efficiency, adopting an integrated solution is a great next step.